MQL technology
Explanations and constraints
Functional principle
Unlike conventional cooling lubricants (Coolants), MQL requires only tiny amounts of lubrication for chip extraction and removal. Applying an optimized lubrication program during the cutting process significantly reduces frictional heat. Moreover, the vast majority of the heat created is carried away with the chip. This effect is further aided by the flowing air current and relatively high feed rates.
MQL processing
These days, production facilities across the globe carry out every imaginable process using MQL systems. A very broad range of different machining operations can be conducted more effectively by replacing conventional flood cooling and lubrication with an optimized MQL lubrication technik.
These include:
- milling
- lathing
- deburring
- thread cutting
- thread moulding
- drilling
- deep-hole drilling
- grinding
- fine boring
- rolling
The two MQL Techniques
The MQL medium can be transported to the cutting edge of the tool in two ways: either externally via spray nozzles or internally – directly to the cutting edge – via the tool’s cooling channels.
Internal MQL supply
Developments over that past two decades have clearly shown that Internal MQl applicationis more effective than external techniques. There are no shadowing effects with an internal MQL supply process. The lubricant applied directly at the cutting edge of the tool and without interference from protrusions caused by nozzles being installed in the machining area. LUBRIX MQL systems have been designed fundamentally with the internal supply of MQL media in mind and fulfil all the demands posed by this technology. Where required, a combined internal and external supply can also be performed using one LUBRIX system.
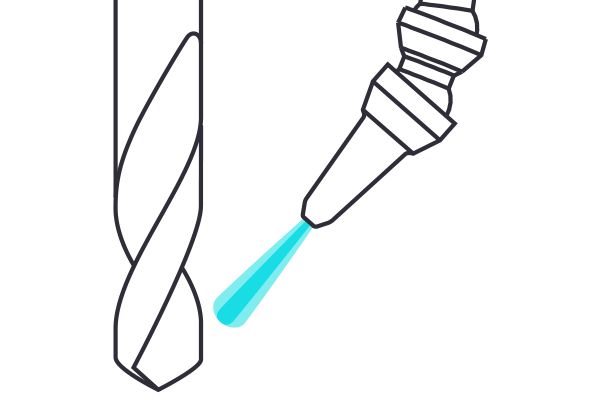
External MQL supply
A nozzle sprays the aerosol onto the cutting edge of the tool’s cutting edge from outside. An external supply is the only option for tools not equipped with cooling ducts. When various tools are in use, one of the biggest challenges posed by this option is ensuring the nozzles are correctly positioned so that the spray consistently hits the proper area of the tool’s cutting edge, a task that also requires extensive manual intervention.
Benefits of the Minimum Lubrication technology
MQL – the economical technology
LUBRIX MQL technology offers numerous advantages compared to conventional manufacturing processes involving cooling lubricant. Lubricating media are prepared as an oil-air mixture (aerosol) inside the LUBRIX MQL systems in such a way that operators always have the option of minimizing the volume of lubricant to be supplied to each individual tool without reducing the tool’s lifetime. Users opting for a LUBRIX MQL system thus profit from many of the above-mentioned potential optimization solutions across the entire production process.